Does my mesh really look OK?
- manchestercfd
- Oct 28, 2016
- 2 min read
In this blog, we will review some key concepts in determining the quality of the mesh used in CFD.
1) Skewness
There are generally two methods for determining the skewness:
Based on the equilateral volume:

• Applies only to triangles and tetrahedrals.
• Default method for tri’s and tet’s.

2. Based on the deviation from a normalized equilateral angle:
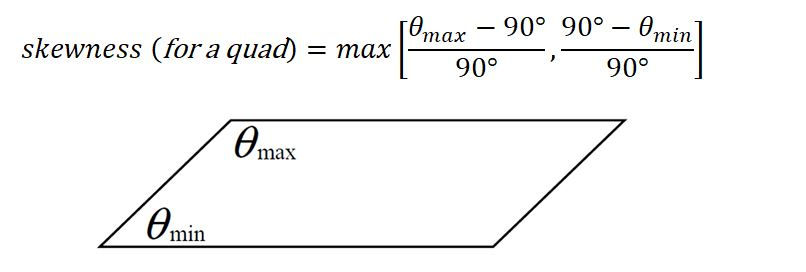
• Applies to all cell and face shapes.
• Always used for prisms and pyramids.
2) Smoothness and aspect ratio
• Change in size should be gradual (smooth).

• Aspect ratio is ratio of longest edge length to shortest edge length. Equal to 1 (ideal) for an equilateral triangle or a square.
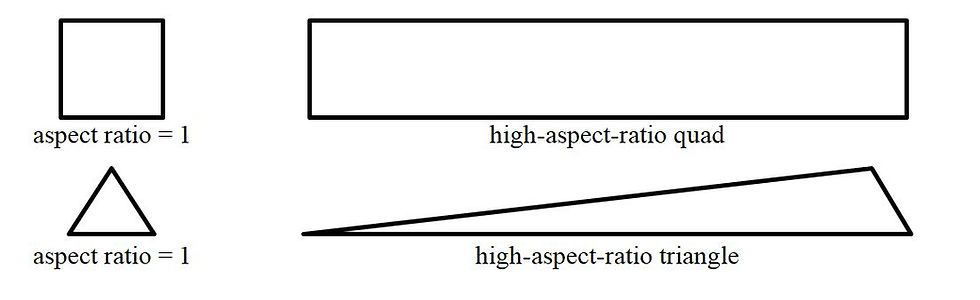
3) Grid Resolution
• Pertinent flow features should be adequately resolved.

• Cell aspect ratio (width/height) should be near one where flow is multi-dimensional.
• Quad/hex cells can be stretched where flow is fully-developed and essentially one-dimensional.

• Ideally, the maximum change in grid spacing should be <20%:

4) Cell counts
• More cells can give higher accuracy. The downside is increased memory and CPU time.
• To keep cell count down:
- Use a non-uniform grid to cluster cells only where they are needed.
- If possible, use solution adaption to further refine only selected areas.
• Cell counts of the order:
- 104 are relatively small problems.
- 105 are intermediate size problems.
- 106 are large. Such problems can be efficiently run using multiple CPUs, but mesh generation and post-processing may become slow.
- 107 are huge and should be avoided if possible. However, they are common in aerospace and automotive applications.
- 108 and more are for specific research topics and are quite rare.
5) Main sources of errors
• Mesh too coarse.
• High skewness.
• Large jumps in volume between adjacent cells.
• Large aspect ratios.
• Inappropriate boundary layer mesh.
• Sharp angles between cells.
• Too many non-matching cells.
Comentários